Injection Molding Color Matching for Cosmetic : Achieving Perfect Colors
Injection molding is one of the most common methods for producing plastic packaging, especially in the cosmetic industry. Whether you're looking to create plastic bottles, bottles, bottles, or jars, color matching plays a critical role in ensuring the final product meets the desired aesthetic and quality standards. When dealing with colorful injection-molded parts, achieving bright colors without any noticeable color differences is a common concern.
Definition of Plastic Color Matching
Plastic color matching refers to the process of blending primary colors—red, yellow, and blue—to create a desirable color that meets color difference requirements, is cost-effective, and remains consistent during processing and use. In addition, color matching can impart additional functional properties to plastics, such as enhancing their light and weather resistance, improving conductivity, or adding anti-static properties. For cosmetic packaging such as skin care bottles, foam bottles, and plastic jars, color matching also plays a key role in branding and product differentiation.
Principles of Color Matching in Cosmetic Packaging
Colors can be categorized into "warm" colors, like red, orange, and yellow, which evoke warmth and joy, and "cool" colors, like blue, green, and purple, which provide a sense of calm. When mixing colors, various methods come into play:
Additive Mixing of Colors and Light: Combining light of different colors to produce new colors.
Color and Pigment Mixing: The process of mixing pigments to create new hues.
Subtractive Mixing of Color Pigments: Mixing primary colors to create intermediate and composite colors.
For example, mixing yellow and blue pigments will produce green, while red and yellow combine to form orange. Understanding these principles is essential for cosmetic packaging manufacturers working with materials such as injection-molded plastic bottles, skin care containers, and cosmetic packaging in general.
Types of Colorants for Cosmetic Packaging
Colorants used in plastic packaging materials for cosmetics can be classified as pigments or dyes, each offering distinct properties:
Pigments: These are insoluble in solvents and must be dispersed mechanically into plastic materials. They come in two types:
Inorganic Pigments: Known for excellent thermal stability and light resistance, they are commonly used in cosmetic packaging materials like plastic bottles, cream jars, and other plastic packaging. However, they are less vibrant than organic pigments.
Organic Pigments: These pigments offer brighter colors but generally have lower heat resistance and weather stability.
Dyes: Organic compounds that are soluble in solvents, dyes offer good transparency and high coloring power, but their small molecular structure can lead to migration issues in some packaging materials, such as plastic lotion bottles or serum bottles.
Specialty Pigments: For added visual appeal, pearlescent pigments, like mica titanium pigments, are often used in cosmetic packaging, especially for luxury items like bottles and high-end skin care bottles.
Color Matching Methods for Cosmetic Packaging
There are several methods for achieving the perfect color in cosmetic packaging, such as for plastic bottles or cream jars:
Direct Addition Method: In this method, color powder is directly mixed with plastic resin. It’s a quick and cost-effective process but often leads to less consistent color results. This method is common in low-cost packaging like basic plastic bottles or injection bottles.
Masterbatch Method: Colorants are pre-mixed into carrier resins to form masterbatches. These masterbatches are then added to the base resin during molding. This method ensures better color consistency and quality control, which is crucial for cosmetic packaging materials like lotion bottles, plastic packaging, and airless containers.
Key Considerations for Color Matching
When performing color matching for cosmetic packaging materials, especially for plastic packaging like plastic bottles, skin care bottles, or foam bottles, several key points must be considered:
Depth of Color: The amount of black or white added to a color influences its depth. For example, in plastic bottles, deeper colors might be used for products like serum bottles or premium cosmetic containers, while lighter shades may be used for more natural skin care packaging.
Color Phase and Hue: Adjusting the hue involves mixing colors in different proportions. For instance, adjusting the shade of a lotion bottle may involve subtle shifts in hue, requiring careful selection of pigments and dyes to ensure the final result matches the desired aesthetic.
Chromatic Aberration: Color differences can be minimized by adjusting the concentration of various pigments and controlling environmental factors such as light exposure during the production process. This is particularly important when manufacturing plastic packaging for skin care, as consumers expect uniformity in color across product lines like serum bottles and cream jars.
Determining the Correct Color Recipe: The correct formula for a desired color involves considering the type and amount of pigment or dye, along with other factors such as the addition of fillers like titanium dioxide to achieve opacity or brightness.
Managing Color Differences in Injection Molding
In the production of cosmetic packaging materials, managing color differences is a common challenge. Several factors can influence the final color of injection-molded plastic products such as plastic lotion bottles, foam bottles, and serum bottles:
Raw Materials: The type of resin and color masterbatch used can affect the final product's color consistency. It's important to source high-quality raw materials to prevent color variation.
Molding Parameters: Injection molding settings like temperature and pressure must be carefully controlled. Variations in these parameters can lead to color inconsistency, which is particularly noticeable in clear plastic bottles or cosmetic containers with detailed designs.
Mixing and Dispersion: Uneven mixing of pigments or masterbatch can result in streaks or color patches in the final product, especially in products with intricate designs or transparent packaging like serum bottles or skin care bottles.
Machine and Mold Factors: Equipment like injection molding machines and molds can also impact the color outcome. Regular maintenance and calibration are essential for achieving consistent color in cosmetic packaging.
Applications in Cosmetic Packaging
In the cosmetic industry, plastic color matching is particularly important for packaging items such as plastic bottles, lotion bottles, serum bottles, and other cosmetic containers. High-quality color matching enhances the visual appeal of the product, aligning with brand identity and consumer expectations.
Whether you are producing plastic packaging for skin care products, airless packaging, or luxury cosmetic items like perfume bottles and cream jars, achieving consistent and vibrant color through proper injection molding color matching is essential for product success. By carefully selecting pigments, controlling the molding process, and using high-quality masterbatches, cosmetic packaging manufacturers can produce attractive and reliable packaging solutions that appeal to consumers and meet industry standards.
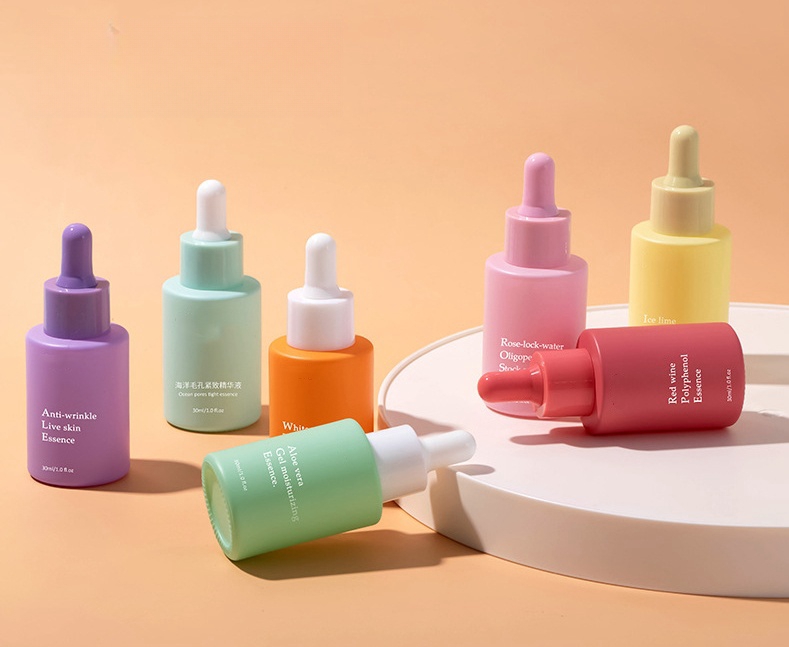